How Rubber Moldings are Made?
Rubber products and components are produced, shaped, and formed using the molding process. The reason for using molding, aside from shaping parts, is to subject the rubber material to chemical processes that toughen or harden the polymer chains of the raw rubber. The chemical reaction forces the long polymer chains to crosslink, which prevents them from moving independently. The rubber material expands and contracts as stress is applied or eliminated.
In the majority of cases, heat is involved in rubber molding to reduce curing time. The three most common types of rubber molding are compression, injection, and transfer. A fourth process, extrusion, is also used to produce rubber parts and components but does not involve using a mold.
How Rubber Moldings Are Made
There are several steps that need to be taken prior to initiating the molding process.
Designing: Rubber can be molded into complex shapes, geometries, and designs. During the design process, configurations are included in the rubber geometry that are used to make the production of the final product more economical. In molding part design, engineers have to account for the parting line and its location, which needs to have a minimum draft angle. The design of the mold is the foundation of part development and can determine the success or failure of the parts production.

Producing the Mold: Once the design is completed, it is transformed into a metal mold. The manufacturing and producing of molds involve the use of hardened steel, beryllium hardened copper, or some forms of aluminum. Steel is the most common material used to make molds since it lasts the longest, which makes it an economical choice even though, initially, it is more expensive. Hardened steel measures 38 to 45 on the Rockwell hardness scale. Included in the construction of the mold are the mold cavity and surface finish of the cavity that has to be correctly adjusted for the proper finish on the final part. The creation of the mold involves the use of computer programs that precisely produce molds that exactly match the parameters of the design. The computerization process cuts down on the amount of time necessary to produce the rubber mold for production. Once the mold has been cast and made, it is tested for dimensional accuracy and compliance with the original design.
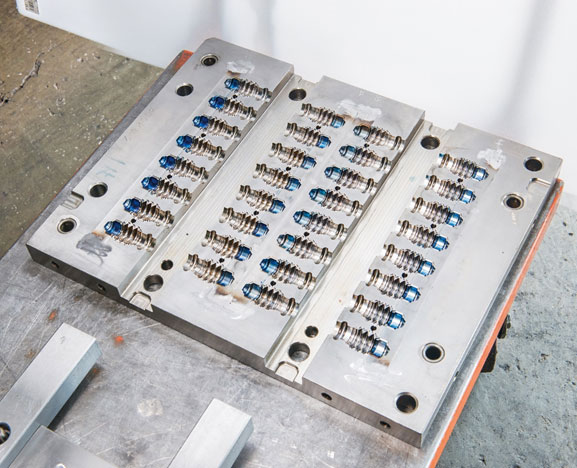
Compression: Compression molding is the simplest type of rubber molding processes. A two part clamshell style mold is used to shape the final part. Once unvulcanized rubber is placed in the mold cavity, the mold is closed and heated. Pressure is applied using a hydraulic press. As the rubber in the mold heats up, it fills the mold cavity. When the proper temperature is reached, the rubber vulcanizes or hardens, which ensures that the rubber will keep its shape as it cools in the mold. The two videos below from REDCO Rubber Engineering and Development Company show the steps of the compression molding process.
The First Part of Compression Molding
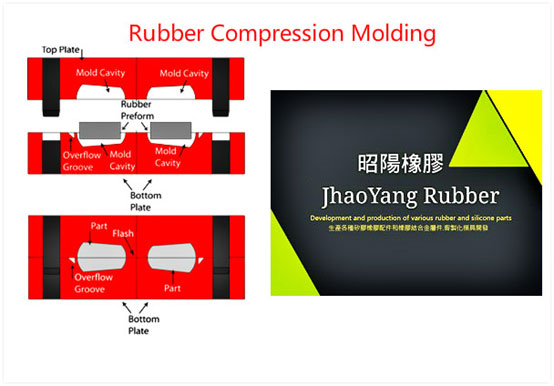
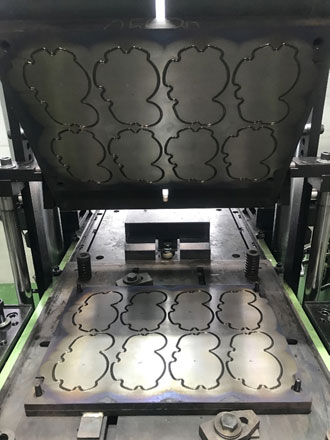
The Demolding Process of Compression Molding
Transfer Molding: The transfer molding process is similar to the compression molding process but uses a transfer system that is on top of the mold that feeds raw rubber into multiple mold cavities after the press has been closed. Before being forced into the mold cavity, the rubber compound is placed in the part of the mold called the pot. From the pot, the compound is forced by a heated plunger or piston into the mold cavity through a small section of the mold called the sprue. Transfer molding is a highly efficient process with short tool loading times. The process allows for high production runs though parts do not have tight tolerances. When curing is completed, the mold is split, and the parts are released. The two videos below from REDCO Rubber Engineering and Development Company provide a short demonstration of the transfer molding process.
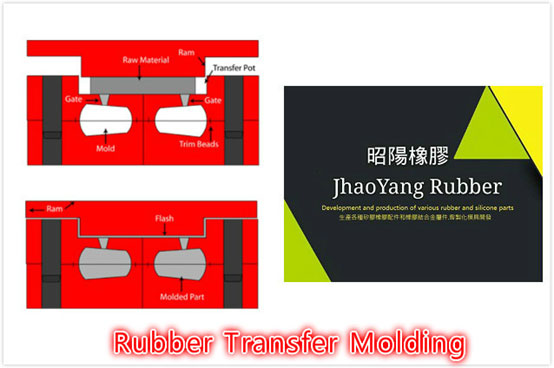
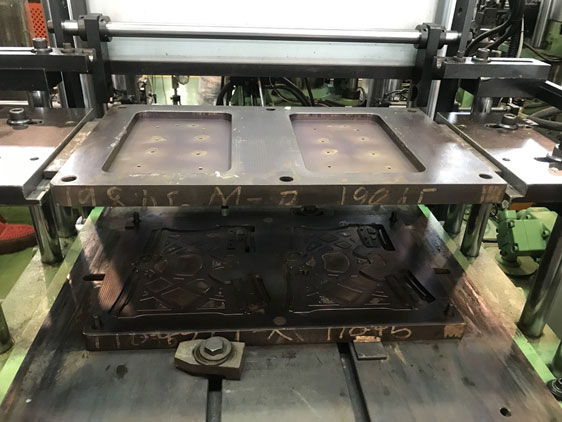
Injection Molding: The injection molding process is used for the production of products that require tight tolerances with high precision and accuracy. The injection process begins by heating raw rubber to form a liquid such that it flows more freely and readily into the mold cavity. The preheating process shortens curing time and allows for higher curing temperatures. The nature of injection molding requires that the mold be tightly clamped, which helps to avoid or limit flashing. The rubber for injection molding is supplied to the mold through a nozzle and barrel assembly that provides a continuous flow. The consistency of the rubber is referred to as gum stock, which enters the mold cavity through a gate after having travelled through a system of sprues and runners. The liquified rubber fills the mold cavity and packs tightly to the walls of the mold to form the desired shape.
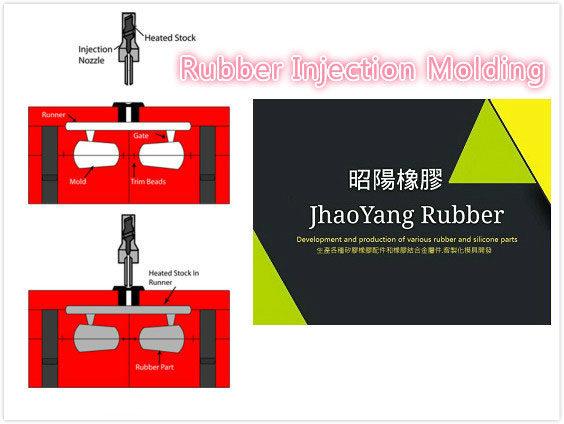
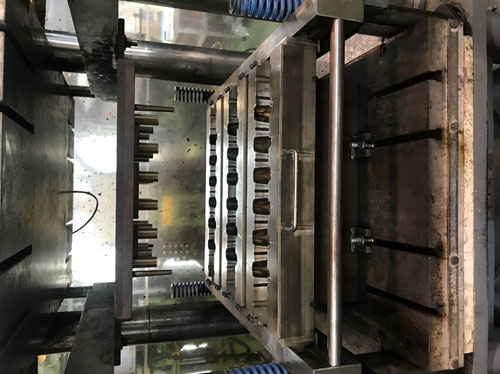
Though injection, compression, and transfer molding are the most common forms of rubber molding, each manufacturer has a different way of completing the process. Regardless of any variations, all rubber molding involves the use of heat and pressure.
- Rubber molding is a process of transforming uncured rubber or an elastomer into a usable product by transferring, compressing, or injecting raw rubber material into a metal mold cavity.
- The most common methods for rubber molding are injection, compression, and transfer.
- Rubber’s flexibility and durability offers engineers different ways to design seals and cushioning components.
- The purpose of the molding process, aside from shaping parts, is to subject the rubber material to chemical processes that toughen or harden the polymer chains of the raw rubber.
- Rubber molding is an essential part of the rubber production industry since components, parts, configurations, and designs can be produced to exactly fit the needs of an application.